Sorting out the gearbox
- cloggymoore
- Aug 8, 2015
- 3 min read
With the gearbox mounting bolts loosened off the 'box' could be twisted / rocked forwards and backwards on the bottom pivot and also up and down, clearly the bolt hole in the bottom of the case was well worn. With the box out the wear was significant. It needed the hole drilling out and a 'bush' pressed in to bring it back to size / correct alignment. The bolt is 3/8 inch so I went for a piece of steel tube 3/8 ID and with a 1/2 outer diameter. The 1/8 increase being enough to remove the ovality of the hole. The pivot bolt was also worn so I replaced that with a new one.
Evidence that the wear in the pivot had also caused the gearbox to be out of alignment with the crankshaft sprocket was shown in that the clutch sprocket had some unusual wear on its rear face caused by the chain side plates. The chain looks OK and I think the teeth will clean up.

Another fault I found was that the large sleeve bolt which secures the crankshaft sprocket and cush drive to the crankshaft had loosened off. This had allowed the cush drive to move out too far resulting in the 'cams' jamming with the spring compressed. So the cush drive was not operating. I know I fully tightened it so it will be 'blue loctited' this time.

In order to make sure the gearbox pivot hole was re-drilled correctly aligned / parallel to the gearbox mainshaft I used my trusty pillar drill with the head rotated 90 degrees to give enough room to get the gearbox below the drill. The pillar drill is mounted on my bench within a degree or two of 'true level'. A 'frame' mounted to the other two gearbox mounting points kept the 'box' rigid and allowed enough adjustment to align the bottom mounting with the drill.

Correct alignment of 'box' and drill bit was achieved using a digital angle measuring device bought on Ebay. The base is magnetic and the method used was to attach it to one side of the drill bit, set it to zero degrees, then mount it on the top of the gerabox sprocket (which should be at 90 degrees to the mounting hole) and adjust the box alignment so the device showed 90 degrees. It was difficlut to get it spot on but I think within half of one degree would be OK. I did this in the fore and aft plane as well.
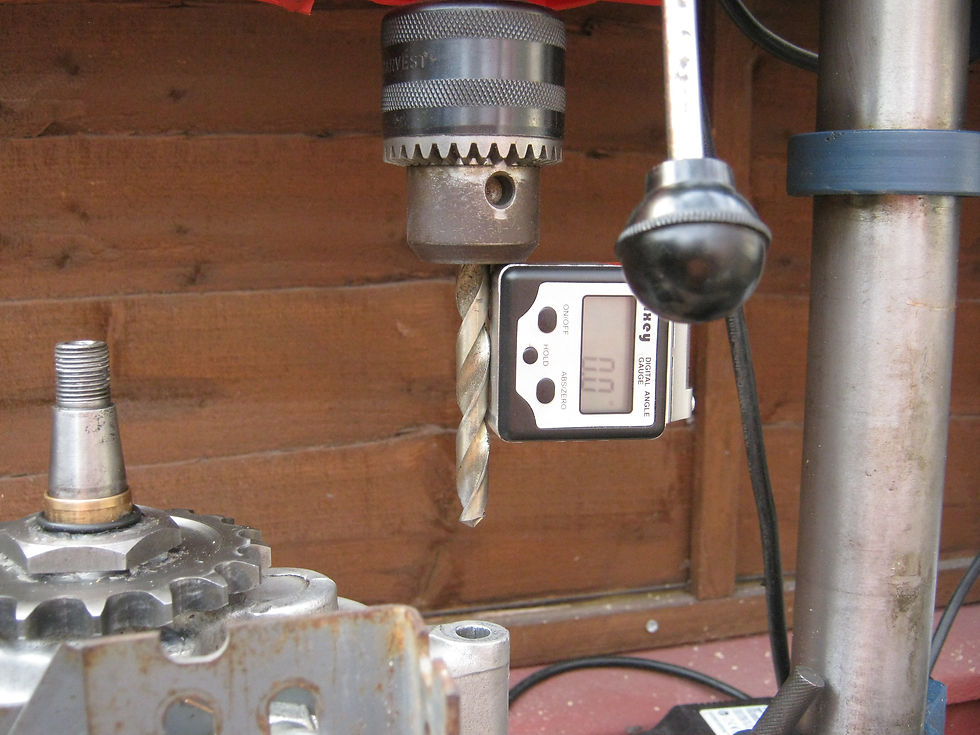
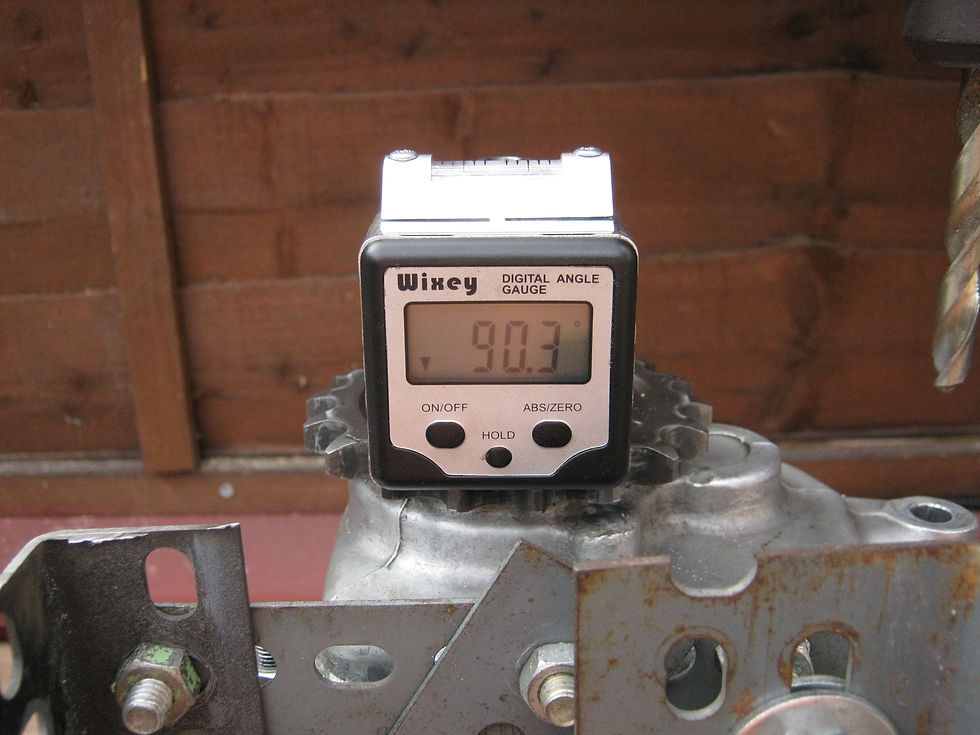
It's then a matter of juggling gearbox position and alignment so the drill is located centrally over the pivot hole. I used a drill that was a close fit in the worn hole (the centre of the hole was less worn so could be used as a guide for the drill). Once it was aligned the drill was changed for the 1/2 inch drill needed for the bush.
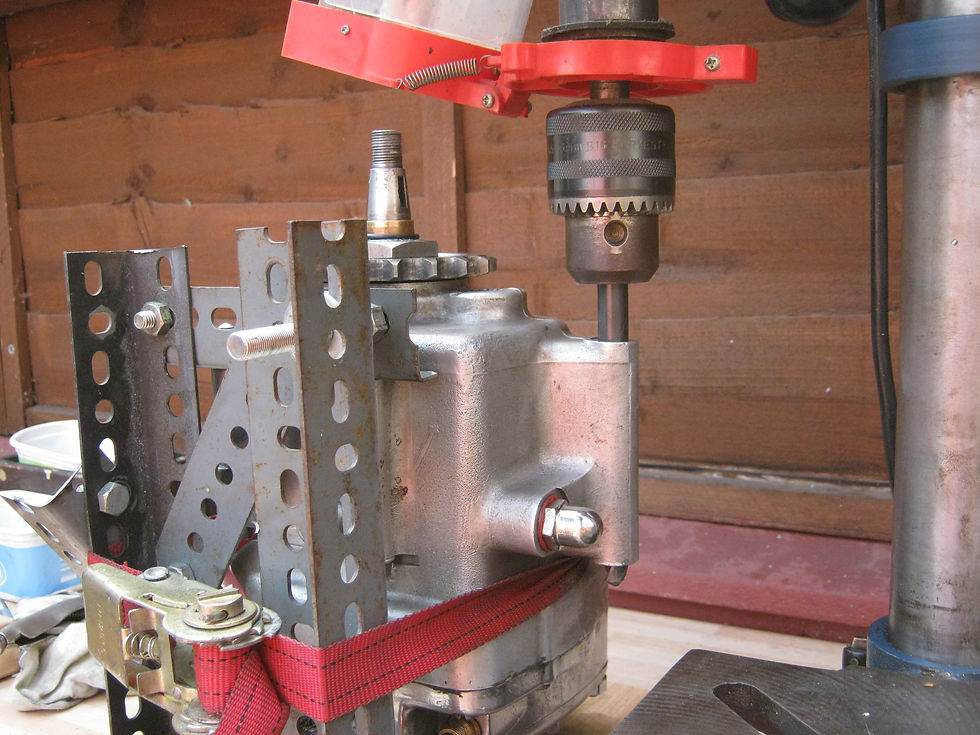
The 'bush was cut to size and, after heating the gearbox up to about 100 degrees Centigrade with a hot air gun, the steel bush was pressed in using a long piece of 'stud' bolt. It was a tight fit but after some more heating it went fully in.
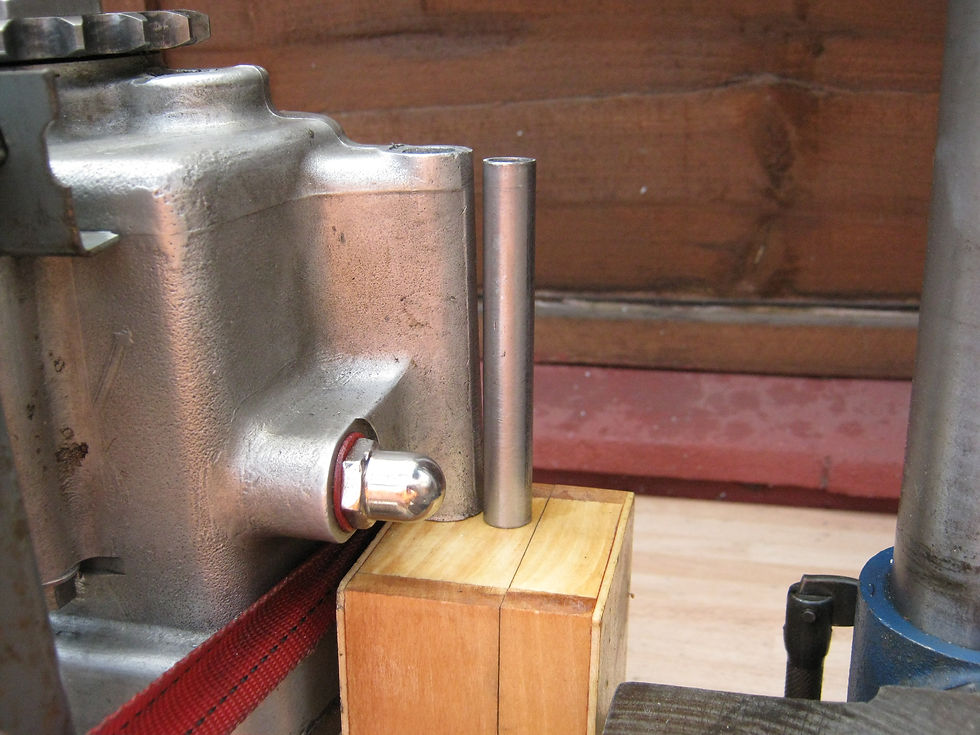
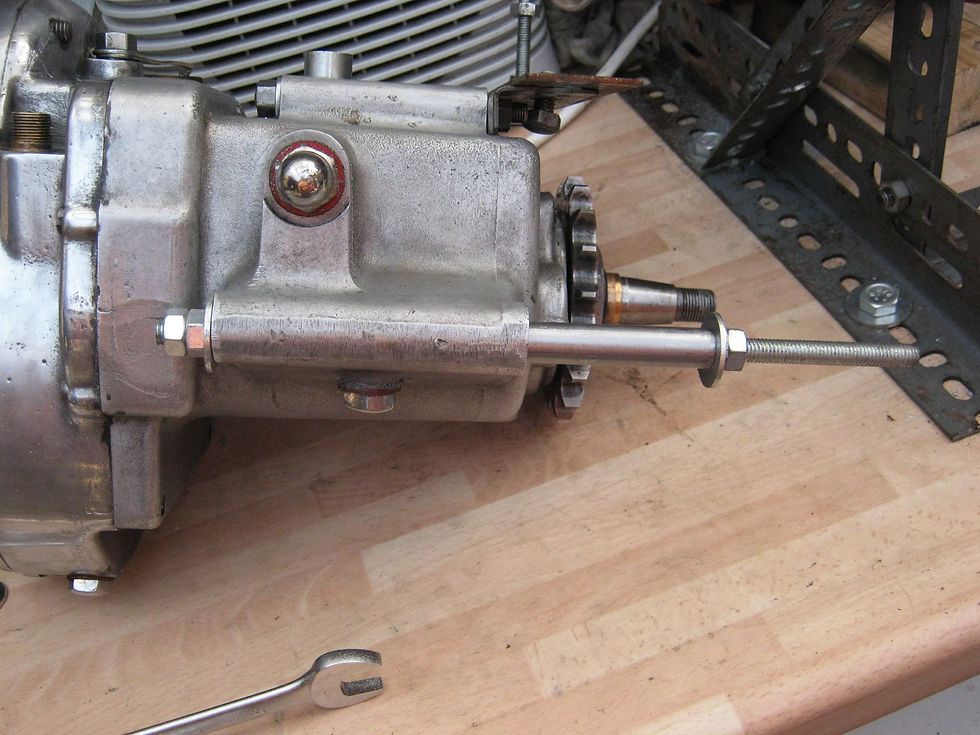
This image shows the new bush in-place. The casing around at the end of the mounting hole had been worn away unevenly where it contacts the mounting lugs on the frame. Both ends were filled flat, washer/s will be used to take up any resulting gap when the box is mounted.

Comments